
If you want to experiment a bit more with PrusaSlicer, try adjusting the Print Settings->Support material->Options for support material and raft->Contact Z distance setting. This might be one area where Simplify 3D has an edge. If you've got a lot of pieces that need large supported areas like this that you can't work-around otherwise, give 'em a shot. Not wrong or right, but their way and less suited for your purpose.
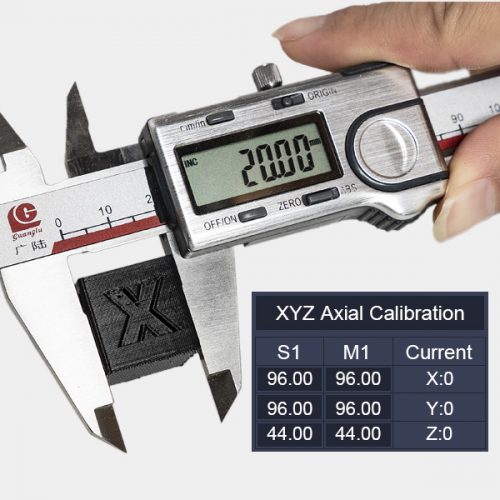
There are myriad reasons for doing it this way that were discussed in the GitHub threads. If you could get rid of the stringy stuff, it would be nearly identical in thickness. Since there is no underlying layer to flatten the bridging layer out, it will add to the thickness of the supported part with that stringy surface you're seeing on the underside that is causing the wall to be roughly one layer thicker. My understanding of the issue with PrusaSlicer/Slic3r supports is that they put down a layer of bridging underneath the supported layer. That said, by all means, try other slicers. I have no idea what the details are, but apparently Tiertime has some patent. OK, that's consistent with what I'd read before. There also seem to be dependencies on bridging parameters, as that stringy stuff between the supported surface and the underlying interface layers is printed as a bridge. One interesting point is that the best Z separation value may vary with layer height. Z distance = Layer Height + 0.1mm), but haven't noticed any superior results. I tried a couple of the variants described in the github threads (e.g. Supports got a lot of attention from the Prusa developers in 2018-2019, but hard to say where it is on the list of priorities. You may see very different results with another slicer, and you may prefer that in this specific circumstance. My understanding is that this approach is worse in some cases, better in others.
#CETUS3D SLICER CODE#
There's actually are several very long discussion of how PrusaSlicer and the Slic3r code base on which it is based on Github. that sure sounds like a limitation of current consumer-grade FFF 3D printing! 😀I'm curious whether the improved Cetus results are the result of their Up Studio (?) software, or a Cura profile.ĭifferent slicers handle bridges differently. I'll print out some samples and post them for comparison. Posted by: Yeah, the problem is that they do sag 😕. Maker's Muse has a good video on this topic.
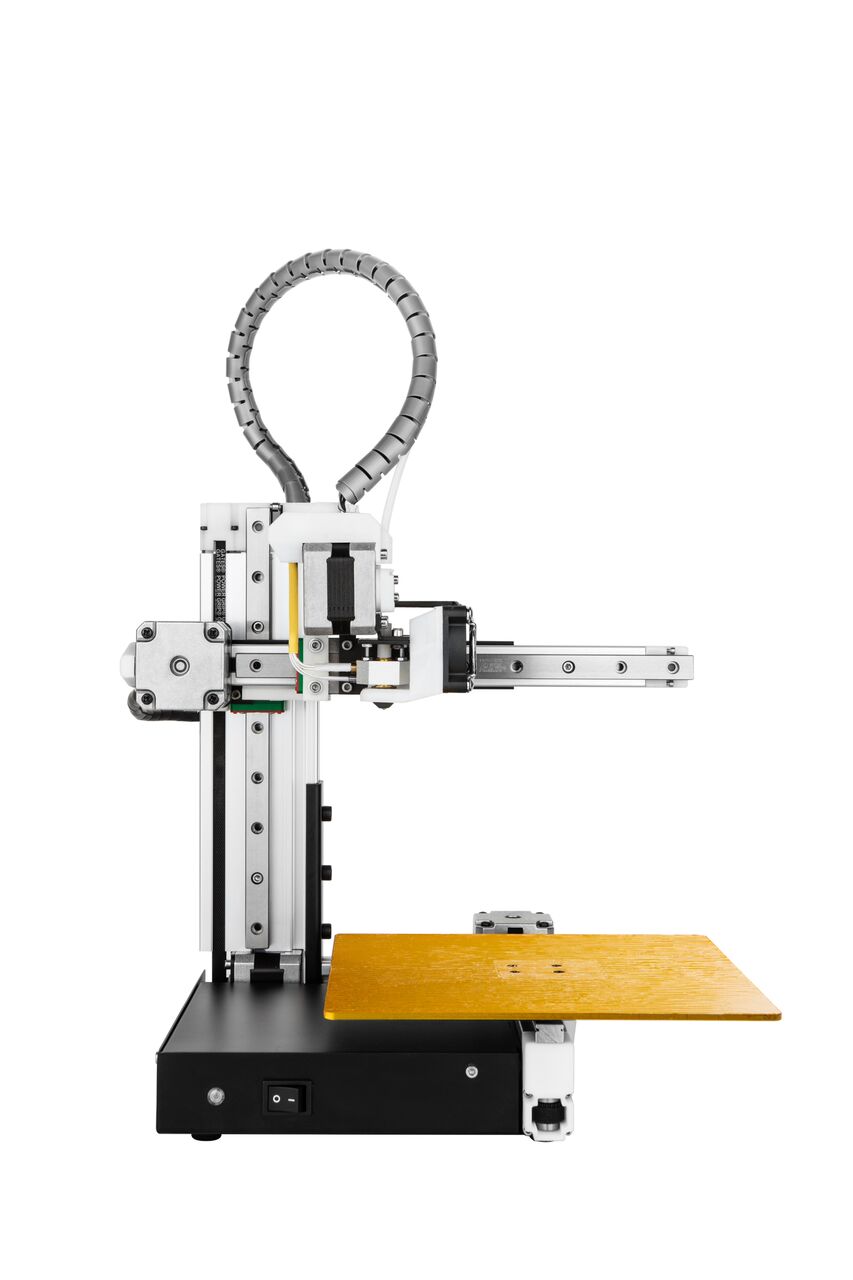
You are running into a limitation of current consumer-grade FFF printing, regardless of manufacturer. There are real world complex parts, where different orientation is not an option.

Posted by: particular part is just for demonstrational purposes, an example.
